Shop Floor Plan
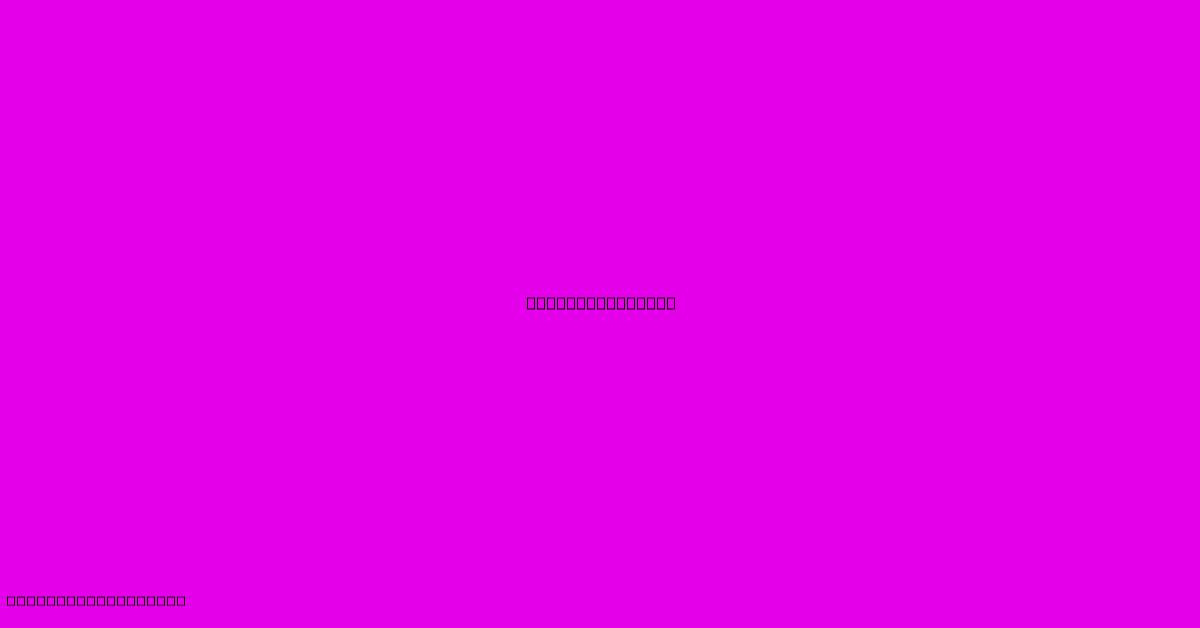
Discover more detailed and exciting information on our website. Click the link below to start your adventure: Visit Best Website meltwatermedia.ca. Don't miss out!
Table of Contents
Unveiling the Secrets to a High-Performing Shop Floor: A Comprehensive Guide to Shop Floor Planning
Editor's Note: This comprehensive guide to shop floor planning has been published today, offering invaluable insights into optimizing your production environment.
Relevance & Summary: Effective shop floor planning is no longer a mere operational detail; it's a strategic imperative. In today's competitive manufacturing landscape, maximizing efficiency, minimizing waste, and ensuring worker safety are paramount. This guide explores the critical aspects of shop floor design, encompassing workflow optimization, equipment layout, material handling, and safety considerations, ultimately leading to improved productivity and profitability. Keywords include shop floor layout, production layout, workflow design, manufacturing efficiency, material handling, workplace safety, lean manufacturing, and 5S methodology.
Analysis: The research behind this guide draws on decades of manufacturing best practices, industry case studies, and expert consultations. It aims to provide a practical and actionable framework for businesses of all sizes, regardless of their industry or production scale. The information presented is designed to empower readers to make data-driven decisions, leading to a more efficient and productive shop floor.
Shop Floor Planning: The Foundation of Manufacturing Excellence
Introduction: The layout of a shop floor significantly impacts production efficiency, safety, and overall profitability. A well-planned shop floor minimizes material handling, reduces bottlenecks, and fosters a safer work environment. This section explores the key aspects of effective shop floor planning.
Key Aspects:
- Workflow Optimization: Designing the flow of materials and processes to minimize movement and waste.
- Equipment Layout: Strategically placing machinery to optimize workflow and minimize travel times.
- Material Handling: Efficient systems for moving materials throughout the shop floor.
- Safety Considerations: Implementing safety measures to protect workers and prevent accidents.
- Space Utilization: Maximizing the use of available space to improve efficiency.
- Flexibility and Scalability: Designing a layout that can adapt to changing production needs.
Discussion:
Effective shop floor planning involves a systematic approach, integrating various elements to achieve optimal results. Let's delve deeper into each key aspect.
Workflow Optimization:
Introduction: Optimizing workflow is crucial for minimizing wasted time and resources. This involves analyzing the sequence of operations, identifying bottlenecks, and eliminating unnecessary steps.
Facets:
- Process Mapping: Visually representing the flow of materials and processes to identify areas for improvement. Examples include using flowcharts or value stream mapping.
- Bottleneck Identification: Pinpointing areas where production slows down due to capacity limitations or process inefficiencies. Risk includes production delays and increased costs. Mitigation strategies include investing in additional equipment or streamlining processes.
- Lean Manufacturing Principles: Applying lean methodologies to eliminate waste and improve efficiency. This includes principles such as just-in-time inventory and kaizen (continuous improvement). The impact is reduced inventory costs and improved overall productivity.
Equipment Layout:
Introduction: The strategic placement of equipment directly impacts workflow efficiency. Careful consideration must be given to the relationship between different machines and processes.
Facets:
- Product Layout: Arranging equipment in a linear sequence based on the manufacturing process. This is suitable for high-volume production with standardized products.
- Process Layout: Grouping similar machines together based on their function. This provides flexibility for handling diverse products.
- Cellular Manufacturing: Organizing equipment into cells that produce complete products or sub-assemblies. This reduces material handling and improves workflow. Risks include increased setup times if not properly managed.
Material Handling:
Introduction: Efficient material handling is essential for minimizing delays and improving overall throughput. This involves selecting appropriate methods and equipment for moving materials throughout the shop floor.
Facets:
- Conveyors: Automated systems for moving materials along a defined path. Examples include roller conveyors, belt conveyors, and overhead conveyors. Impacts include increased efficiency and reduced labor costs.
- Forklifts: Versatile equipment for moving pallets and other heavy materials. Risks include accidents if not operated safely. Mitigations involve rigorous training and safety protocols.
- Automated Guided Vehicles (AGVs): Robots that navigate the shop floor autonomously, transporting materials without human intervention. Impacts include increased efficiency and reduced labor costs.
Safety Considerations:
Introduction: Prioritizing safety is paramount in any shop floor design. A safe work environment reduces the risk of accidents, protects workers, and improves productivity.
Facets:
- Ergonomics: Designing workstations to minimize strain and fatigue. Examples include adjustable chairs and work surfaces.
- Machine Guarding: Protecting workers from moving parts of machinery. Impacts include reduced workplace injuries and improved worker morale.
- Emergency Exits and Safety Equipment: Ensuring easy access to emergency exits and providing readily available safety equipment such as fire extinguishers and first-aid kits. Risks include delays in evacuations in case of emergencies. Mitigations include regular safety drills and clear signage.
Space Utilization:
Introduction: Maximizing the use of available space is crucial for improving efficiency and reducing costs. This involves optimizing the arrangement of equipment and materials.
Facets:
- 3D Modeling: Utilizing 3D software to visualize the shop floor layout and optimize space utilization. Impacts include improved planning and reduced errors.
- Vertical Space Utilization: Utilizing vertical space for storage and equipment placement to maximize floor area. Risks include difficulties in access and increased safety concerns. Mitigations involve proper shelving systems and safety training.
Flexibility and Scalability:
Introduction: Designing a shop floor that can adapt to changing production needs is crucial for long-term success. This involves considering future expansion and potential changes in production processes.
Facets:
- Modular Design: Utilizing modular equipment and layouts that can be easily reconfigured. Impacts include adaptability to changing production requirements.
- Future Planning: Incorporating future expansion needs into the initial design to avoid costly modifications later. Risks include underestimation of future needs. Mitigations involve robust forecasting and scenario planning.
FAQ
Introduction: This section addresses frequently asked questions regarding shop floor planning.
Questions:
- Q: What is the most important factor to consider when planning a shop floor? A: Workflow optimization is arguably the most crucial factor, as it directly impacts efficiency and productivity.
- Q: How can I determine the optimal layout for my shop floor? A: Analyzing production processes, material flow, and equipment requirements is crucial to choosing the optimal layout (product, process, or cellular).
- Q: How can I improve material handling efficiency? A: Implementing automated systems like conveyors or AGVs can significantly improve efficiency and reduce labor costs.
- Q: What are the key safety considerations for a shop floor? A: Prioritizing ergonomics, machine guarding, and providing easy access to safety equipment are paramount.
- Q: How can I ensure my shop floor is scalable and flexible? A: Adopting modular designs and considering future expansion needs during the planning phase is crucial.
- Q: What software can assist with shop floor planning? A: Several software options, including CAD and 3D modeling programs, offer features specifically designed for shop floor layout design.
Summary: Effective shop floor planning is a multi-faceted process that integrates workflow optimization, equipment layout, material handling, and safety considerations. A well-planned shop floor leads to increased productivity, reduced waste, and a safer work environment.
Closing Message: Investing in a well-planned shop floor is an investment in the future of your manufacturing operations. By implementing the strategies outlined in this guide, businesses can unlock significant improvements in efficiency, profitability, and worker satisfaction. Proactive planning, continuous improvement, and employee engagement are key to long-term success.
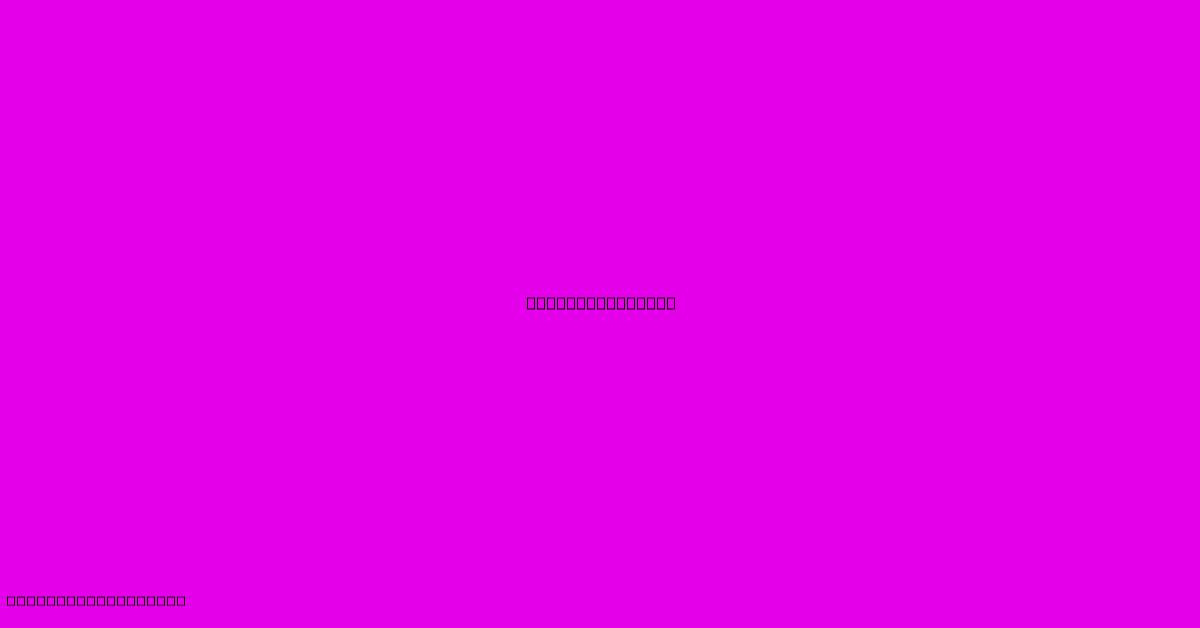
Thank you for visiting our website wich cover about Shop Floor Plan. We hope the information provided has been useful to you. Feel free to contact us if you have any questions or need further assistance. See you next time and dont miss to bookmark.
Also read the following articles
Article Title | Date |
---|---|
Moisture Barrier For Laminate Flooring | Jan 03, 2025 |
16x40 Cabin Floor Plans | Jan 03, 2025 |
Floors Direct Reviews | Jan 03, 2025 |
Wooden Floor Paint | Jan 03, 2025 |
Computer Desk Floor Mat | Jan 03, 2025 |