Osha Floor Marking Requirements
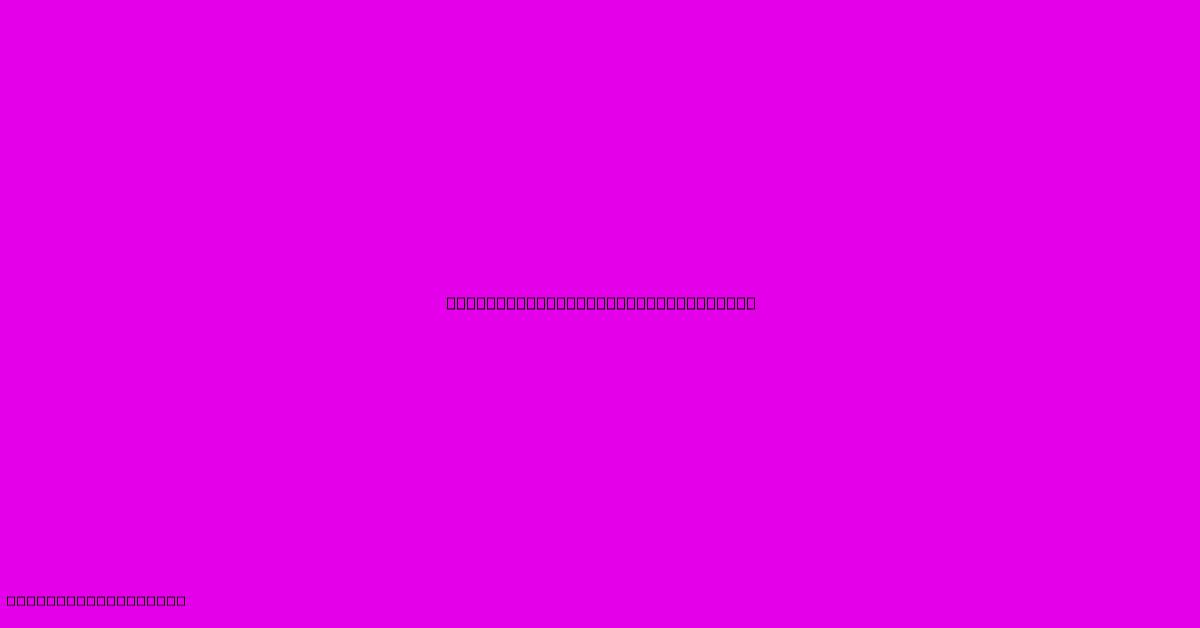
Discover more detailed and exciting information on our website. Click the link below to start your adventure: Visit Best Website meltwatermedia.ca. Don't miss out!
Table of Contents
OSHA Floor Marking Requirements: A Comprehensive Guide to Workplace Safety
Hook: Do clear floor markings significantly reduce workplace accidents? Absolutely. Implementing a robust floor marking system is not just a best practice; it's a crucial element of maintaining a safe and compliant workplace, as mandated by OSHA.
Editor's Note: This comprehensive guide to OSHA floor marking requirements has been published today to provide businesses with the knowledge to create safer work environments.
Relevance & Summary: Workplace accidents resulting from slips, trips, and falls constitute a significant portion of workplace injuries. OSHA floor marking requirements play a vital role in mitigating these risks by providing clear visual cues for pedestrian and vehicular traffic flow, hazard zones, and emergency exits. This guide summarizes OSHA's guidelines on floor marking, encompassing materials, color codes, placement, and maintenance, offering a complete understanding of compliance and best practices. Semantic keywords include: workplace safety, floor marking, OSHA compliance, safety regulations, hazard identification, visual cues, pedestrian safety, forklift safety, aisle marking, industrial safety, facility safety.
Analysis: This guide is based on a thorough review of OSHA's standards, best practices in industrial safety, and expert opinions in workplace safety management. The information aims to provide a practical and actionable framework for businesses of all sizes to effectively implement and maintain OSHA-compliant floor marking systems. The analysis includes considerations for various work environments, including manufacturing facilities, warehouses, construction sites, and offices.
Subheading: OSHA Floor Marking Requirements
Introduction: OSHA doesn't have a single, dedicated standard solely for floor markings. However, several regulations indirectly address the need for clear and effective floor marking systems as a crucial component of overall workplace safety. These regulations fall under the broader umbrella of hazard communication, general industry standards, and specific requirements related to material handling and storage.
Key Aspects:
- Hazard Communication: OSHA's Hazard Communication Standard (29 CFR 1910.1200) mandates that employers inform employees about workplace hazards, including those indicated by floor markings.
- Walkways and Passageways: General industry standards (e.g., 29 CFR 1910.22) require employers to maintain safe walkways and passageways, free from obstructions, and properly marked to ensure pedestrian safety.
- Material Handling and Storage: Regulations concerning material handling and storage (e.g., 29 CFR 1910.176) often necessitate floor markings to delineate storage areas, traffic aisles, and restricted zones.
- Emergency Exits: OSHA standards require clearly marked and unobstructed emergency exits (e.g., 29 CFR 1910.36). Floor markings play a significant role in guiding employees to these exits during emergencies.
Discussion: The absence of a specific floor marking standard doesn't imply a lack of requirements. OSHA's general duty clause (29 CFR 1910.11(b)) mandates employers to provide a safe and healthful work environment, and effective floor marking is a significant aspect of fulfilling this obligation. The effectiveness of floor marking directly impacts employee safety and compliance with numerous other OSHA standards.
Subheading: Color Coding and Symbol Usage
Introduction: Consistent color coding is essential for effective floor marking. While OSHA doesn't mandate specific colors, the industry has widely adopted a standard color code system for clarity and consistency.
Facets:
- Yellow: Used to delineate pedestrian walkways, designating safe pathways for employees to navigate. This is crucial for separating pedestrian traffic from vehicular traffic in high-traffic areas.
- Red: Indicates danger or prohibited areas, including emergency equipment locations, fire protection equipment, and hazardous materials storage zones. This color immediately warns employees of potential risks.
- White: Often used to create lines defining aisles and traffic flow for vehicles such as forklifts. This helps ensure that pedestrians and vehicles maintain safe distances.
- Blue: Frequently used to designate safety equipment storage locations like first-aid kits or emergency eyewash stations. This makes crucial safety resources readily identifiable.
- Green: Typically used to mark safe areas, such as first-aid rooms or designated smoking areas (if permitted). This assists in easy location of designated areas.
Summary: Consistent and standardized color coding simplifies hazard identification, improving employee understanding and reducing the likelihood of accidents. This ensures that critical safety information is readily available and easily understood.
Subheading: Material Selection and Application
Introduction: The choice of materials for floor marking significantly influences its durability and visibility.
Further Analysis: Tape, paint, and stencils are common options. Tape offers flexibility and ease of application but may have shorter lifespans in high-traffic areas. Paint offers better durability but requires more preparation and application time. Stencils facilitate creating uniform markings, particularly for complex designs or symbols. The choice of material should consider the specific environment's conditions (e.g., exposure to chemicals, heavy traffic, temperature fluctuations).
Closing: Selecting appropriate materials for floor marking is crucial for long-term effectiveness and ensures safety markings remain visible and legible, preventing accidents.
Subheading: Maintenance and Regular Inspection
Introduction: Maintaining floor markings is crucial for sustaining a safe workplace.
Further Analysis: Regular inspections should be conducted to identify worn-out or damaged markings. Prompt repair or replacement ensures the continued efficacy of the safety system. The frequency of inspection will depend on the intensity of use in different areas. A well-defined schedule is crucial to help ensure safety is always a top priority.
Closing: Neglecting maintenance can compromise the effectiveness of floor markings, leading to accidents. A proactive maintenance schedule is an integral part of an effective safety program.
Subheading: FAQ
Introduction: This section addresses frequently asked questions regarding OSHA floor marking requirements.
Questions:
- Q: Are there specific OSHA standards solely dedicated to floor marking? A: No, but several general industry standards indirectly address the need for effective floor marking for workplace safety.
- Q: What are the consequences of non-compliance? A: Non-compliance can result in citations, penalties, and potential legal liabilities.
- Q: How often should floor markings be inspected? A: Inspection frequency depends on the level of traffic and wear in the areas but should be regular to guarantee visibility and prevent accidents.
- Q: Can I use any color for floor markings? A: While OSHA doesn't mandate specific colors, adopting industry-standard color codes is recommended for clarity and consistency.
- Q: What types of materials are suitable for floor markings? A: Tape, paint, and stencils are common options, with the selection depending on the environment and anticipated wear.
- Q: Who is responsible for ensuring floor markings are maintained? A: The employer has the ultimate responsibility to maintain a safe workplace, including maintaining effective floor markings.
Summary: Understanding OSHA's implications regarding floor marking and addressing common concerns contributes significantly to a safer workplace.
Transition: Following best practices for floor marking complements other safety measures.
Subheading: Tips for Effective Floor Marking
Introduction: These tips enhance the effectiveness of your floor marking system.
Tips:
- Conduct a thorough workplace assessment: Identify all potential hazards and areas requiring marking.
- Use clear and consistent color coding: Adhere to industry standards for optimal communication.
- Employ high-visibility materials: Choose durable materials appropriate for the work environment.
- Maintain clear visibility: Regularly inspect and replace worn-out markings.
- Provide employee training: Ensure employees understand the meaning of floor markings.
- Document your floor marking plan: This is crucial for auditing and ensuring consistent application.
- Consider using additional safety measures: Supplement floor markings with other safety precautions.
- Stay updated on OSHA regulations: New guidelines and interpretations may affect floor marking practices.
Summary: Implementing these tips significantly contributes to establishing a safer and more compliant workplace.
Transition: This guide provides a comprehensive overview of OSHA floor marking requirements.
Summary: This article provided a comprehensive exploration of OSHA floor marking requirements, emphasizing their significance in maintaining workplace safety. Key aspects covered include color coding, material selection, maintenance, and practical tips for implementation.
Closing Message: Prioritizing safety through effective floor marking systems is not just a legal requirement; it's an investment in employee well-being and a commitment to a productive and incident-free workplace. Regular review and updates to your floor marking system are essential for maintaining a safe work environment.
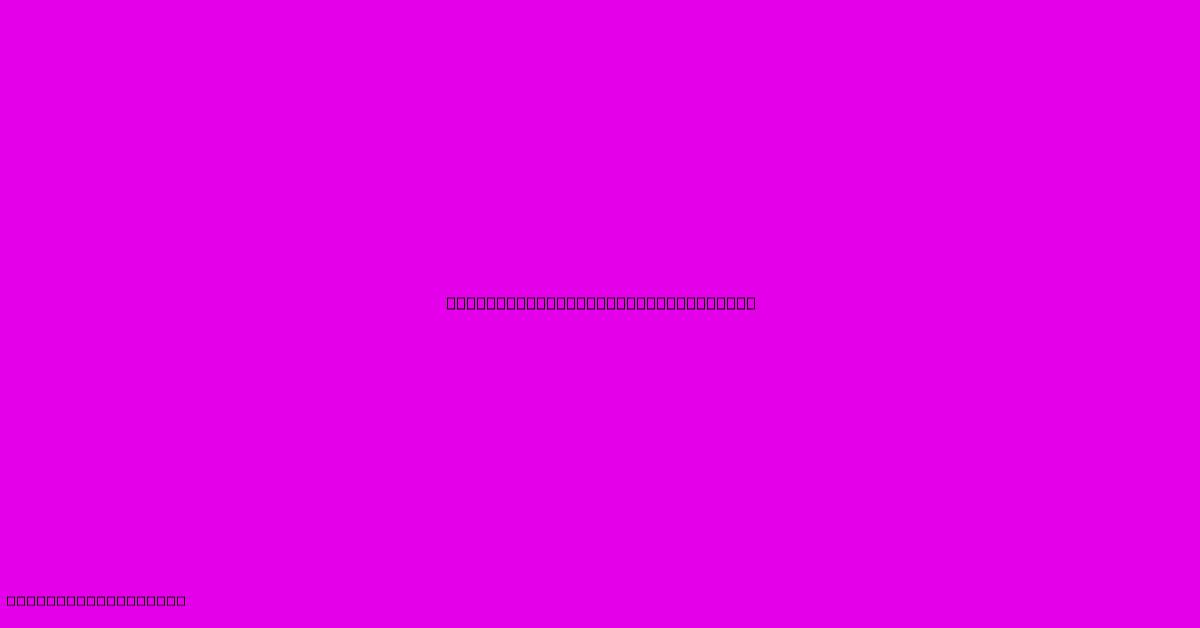
Thank you for visiting our website wich cover about Osha Floor Marking Requirements. We hope the information provided has been useful to you. Feel free to contact us if you have any questions or need further assistance. See you next time and dont miss to bookmark.
Also read the following articles
Article Title | Date |
---|---|
Grout On Shower Floor | Jan 04, 2025 |
Is Laminate Flooring Cheaper Than Carpet | Jan 04, 2025 |
Engineered Hardwood Flooring Sale | Jan 04, 2025 |
Floor Under Layment | Jan 04, 2025 |
How Much Does It Cost To Re Sand Hardwood Floors | Jan 04, 2025 |